Great music draws us in, and the phenomenal gear that presents it beckons just as convincingly. As one of the Product Specialists at World Wide Stereo, I was afforded the incredible opportunity to get an in-depth education on all things McIntosh from their top specialists, and experience firsthand just what makes them special. McIntosh Laboratories is a music Mecca and, in retrospect, my trip to their headquarters in Binghamton, NY certainly did feel like a necessary pilgrimage.
I’ve been to many manufacturing facilities in my life across many
industries audio-related and beyond, but there was something completely unique
and special about how McIntosh does things. I’ve never seen a facility staffed
by such dedicated craftsmen and craftswomen, not only assembling, but truly building
these units from the ground up. This is an American product from beginning to
end, and the resulting quality shows the moment your eyes fall on the finished
machines. I’d like to share this with you: a brief synopsis of my trip, and a
peek inside a great American company.
Day 1: The history of McIntosh Labs.
After a good night’s sleep at a hotel near the McIntosh facilities, I awoke and joined the congregating group in the lobby. Dealers from every corner of the country had gathered: some who’ve sold this product for years, and some who were recently approved to be authorized dealers. One of the most remarkable things about this industry is the diversity of its constituents, and this group was no exception.
Ken Zelin (a McIntosh expert AND World Wide Stereo sales specialist) greeted us and distributed name tags. We made our casual acquaintances with each other and boarded the buses that would bring us to McIntosh Labs. We arrived moments later at the doorstep of an impressive three-story building with black glass covering the façade, adorned with the iconic globe of McIntosh Labs. We entered beneath and were met by a wonderful receptionist who welcomed us warmly. With a motherly gesture toward the left, she showed that cookies and coffee were available for us in a nearby break room. However, this was not the time for breaks.
Session one began almost immediately. We shuffled into the training room to find our seats. A brief history of the company introduced us to a rather unofficial mission statement: McIntosh does not build equipment and ask the world to accept it — they ask what their customers want, and then they build it with the best performance that can be managed. For a titan of this industry, the company and staff are quite casual and friendly. Being there was like returning to a rural childhood hometown after years of living in a crowded city.
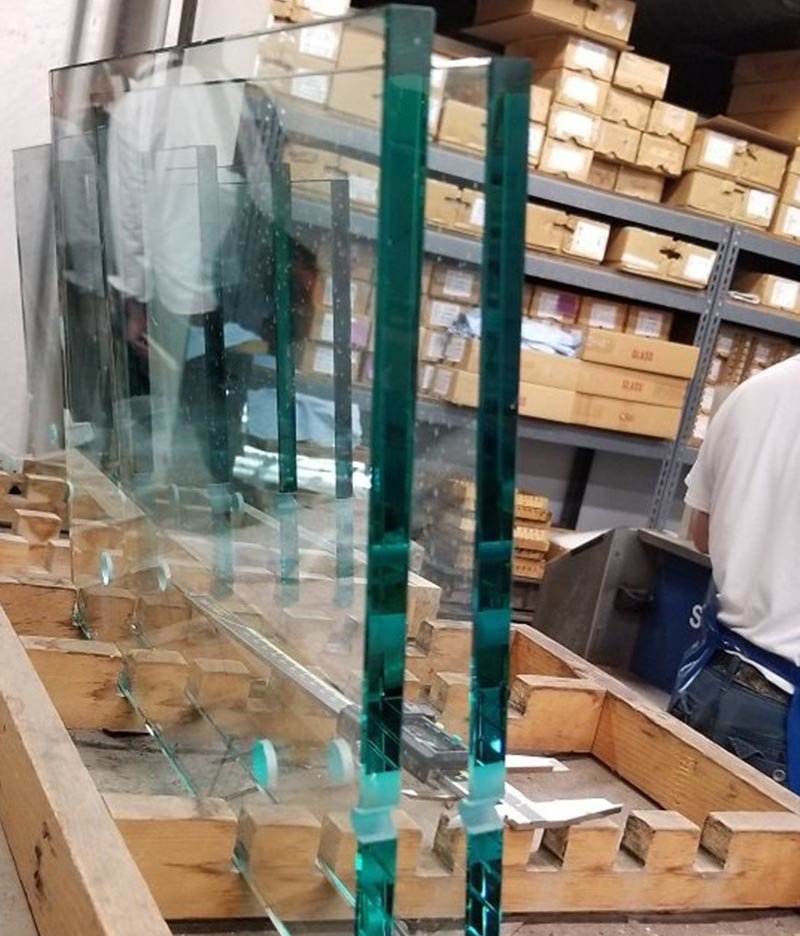
Touring the manufacturing facilities.
After the history lesson, it was time for a tour of the manufacturing facilities. This wasn't the first factory I’ve toured, but I was immediately grinning from ear to ear. I love machinery and seeing huge bins of parts — watching the assembly of world-class product is far from dull, in my opinion. However, I was a bit surprised by what I found. Here, there are no huge bins of parts waiting to be assembled: only the base materials themselves, which are constructed by hand to make each part. There is hardly any machinery at all – only in places where human hands are not adequate (such as glass cutting). Even then, the machines are manually operated and don’t rely on computers to drive them. The wonderful employees are not assembly line workers, but skilled craftsmen and craftswomen. I was extremely impressed by the skill, care, and dedication to perfection shown by every worker.
My favorite part of the tour was watching the process by which the famed glass faceplates are built. Cut from raw sheets of glass, they start with a water cutter. High pressured water fires in a jet, slicing through the glass like butter. However, it isn’t just water – mixed into the H2O is powder from crushed garnet, a stone crystal that has been used as an abrasive since the Stone Age. Adding this fine, sandy material ensures extremely precise, clean cuts that don’t create micro-shatters in the glass (which pure water would leave behind).
Then, using a brand new printing system (a dramatic improvement over the older silk-screening technique), special paints are applied to the backside of the glass, adding the signature McIntosh look. A unique feature of this new technique: the McIntosh logo, proudly scripted in large font on the glass, has the signature gold color. When illuminated by a backlight, however, it glows the brilliant, signature green color.
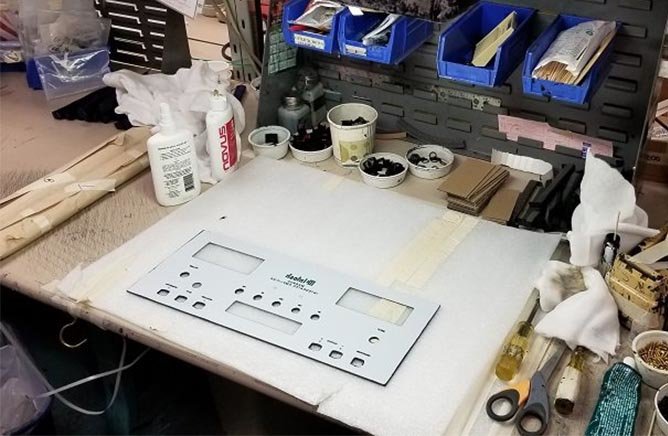
A glass faceplate ready for final touch-ups
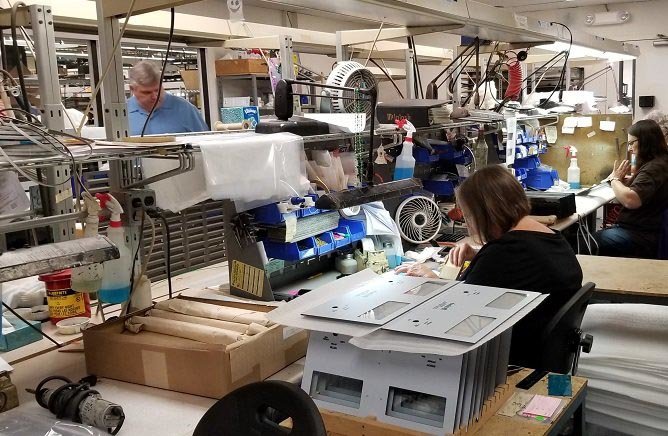
McIntosh employees finish glassplates by hand

A proud employee shows off the final product
Next up: McIntosh amplifiers.
Once the tour had ended, it was back to the classroom for an in-depth lecture on the technical aspects and attributes of McIntosh stereo amplifiers, followed by another lecture on preamplifiers. The amount of detail and ingenuity that goes into the engineering and design of these products is astounding and so detail-intense — but not everything about amplifiers is glamorous.
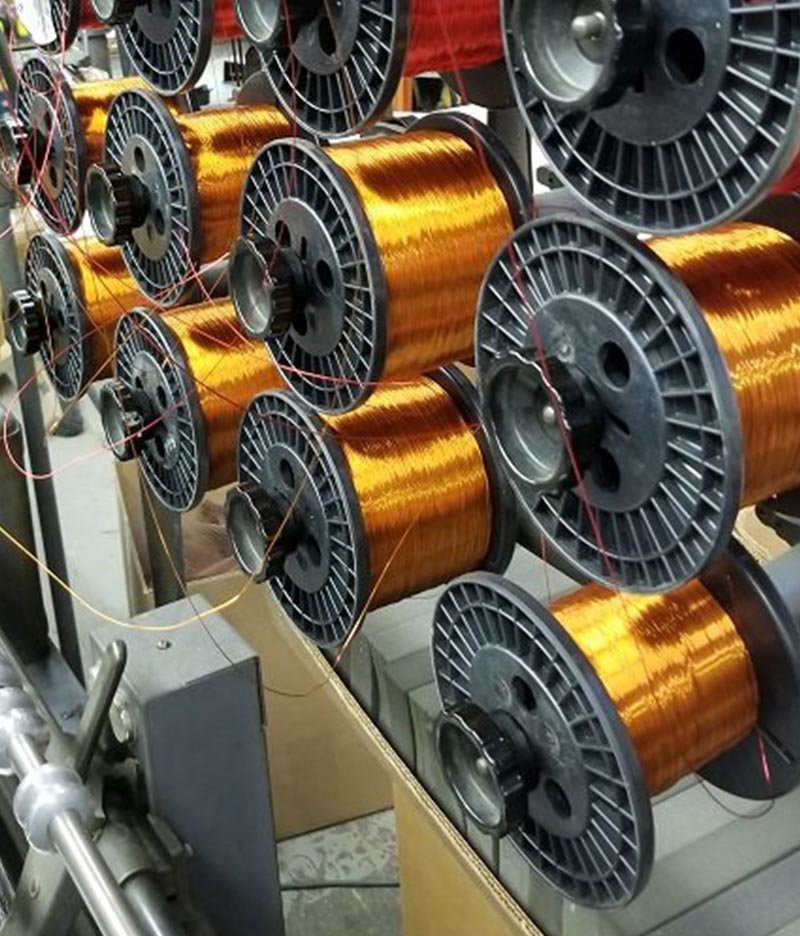
At a glance, some amplifiers seem to be entirely mundane, but deeper inspection reveals a well-thought purpose and brilliant design. Take, for instance, McIntosh's patented Autoformer technology, which is used in their best amplifiers so they can power almost any speaker in the world. Hand-wound transformers (made with different colored wire, as seen in the photo) are placed inside heavy metallic domes. Then, they are filled with tar for ultimate isolation and insulation. This is far more than copper strands and distilled coal residue, though. Autoformers play an important role in the amplifier's ability to supply plenty of robust power to any speaker, regardless of impedance. Whether you have efficient 8 ohm speakers or electrostats that can dip as low as 2 ohms, McIntosh amplifiers don't even blink.
Traditional amplifier design, on the other hand, forces the engineer to choose a specialty: amps
that can handle low impedances usually perform best within a specific range of
impedance. With Autoformers, a McIntosh amp can transform its own inner
circuitry, allowing it to specialize in whatever speaker you have (or will
have) for the rest of your life!
McIntosh amps have a reputation for lasting 30+ years without significant loss in performance, and are built with the same old-world quality as they were back in the 1940s. As a result, most McIntosh customers will go through multiple pairs of speakers before getting a new amplifier — and it's the Autoformer that gives them complete freedom in the speakers they choose. In fact, McIntosh life expectancy is so long, we often call them "the cheapest amp you can buy," because you'll run through the lifetimes of six $1,000 receivers long before a $6,000 McIntosh bites the dust.
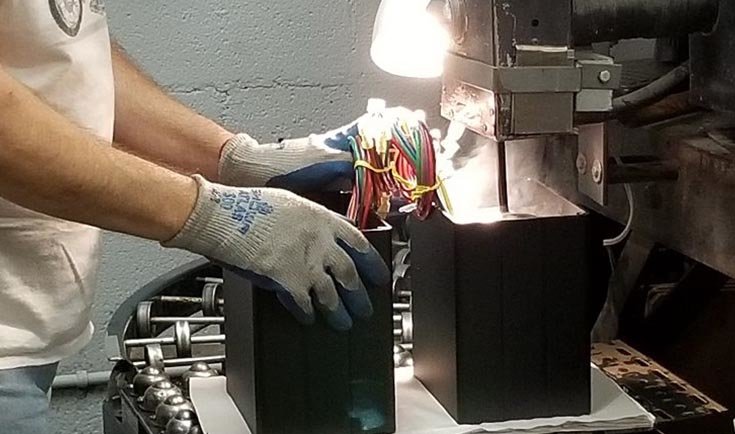
Hot liquid tar is poured into a brand new Autoformer to hold everything in place
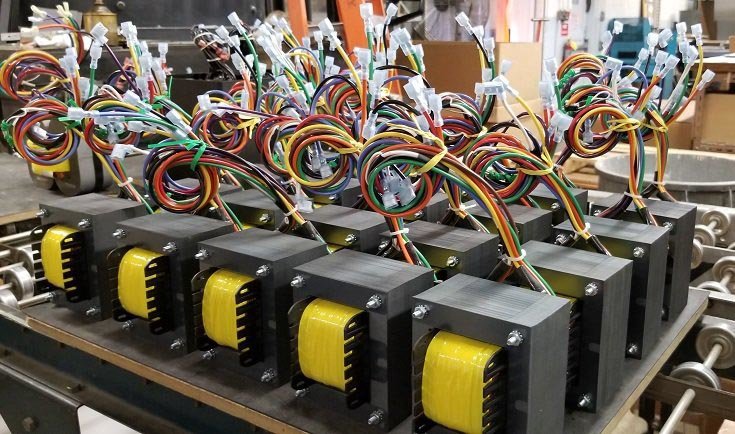
Transformers awaiting their final home in the tar-filled Autoformer
Once we wrapped up the amplifier session of the day, a bus ride brought us back to the hotel for a lovely dinner and evening together, where we each excitedly discussed the things we had seen and learned.
Day 2: Studies on McIntosh integrated amps, music sources, & speakers.
We awoke the next morning and gathered as we had before. Again we rode the bus, and again we took our seats in the classroom. We began with a study of McIntosh's integrated amplifiers, which, to their credit, are generally built with all the same concepts, features, and capabilities as their separated brethren.
Turntables, CD players, streaming players - oh my!
After integrated amplifiers, we moved on to music sources: turntables, CD players, and streaming players. The same attention to detail and dedication to performance shone through in this category as well. While streaming audio is clearly the future of music listening, CD players remain in high demand (even these more expensive audiophile options). McIntosh does not build the players because they are the future, but because the majority of their customers have massive CD collections accumulated over the decades. McIntosh does not ask their customers to throw those away. Instead, they faithfully build units that allow their adoring customers to keep listening to their favorite albums, however they may be stored.
At last, time for speakers!
This was one of the more interesting categories to study, because the philosophy behind McIntosh speakers is very different from competitors’ offerings at similar price points. While most manufacturers chase an ideal perfection in sound, McIntosh simply wants a speaker that can handle exorbitant amounts of power. Why? Because their customers want it. Suddenly, the mantra we learned on day one was beginning to come into focus. When you build spectacular amplifiers with 400, 600, or even 1200 watts per channel, it’s hard to find a speaker that can handle that much juice without simply melting. Keep the volume knob low, and you are good to go — but where’s the fun in that? Even if your system rips and roars at 10% of the total available power, it just isn’t as fun as watching those glowing blue meters dance at the top of the scale. Enter the McIntosh speaker line. They’re not inefficient, they are just masterfully built to reach audiophile quality sound while making proper use of every bit of those 1200 watts.

The crowning moment of training: A tour of the engineering facilities.
Naturally, most of what we saw and experienced is highly confidential, and I hesitate to go into too much detail in my description. Suffice it to say that we experienced some very cool new products, and the future for McIntosh appears very bright, indeed. Additionally, we got to experience their echoic and anechoic chambers (pictured). In case you're unfamiliar with what this does, an anechoic chamber is a room designed to eliminate echoes and completely absorb sound. Any reflections of sound are trapped and absorbed by large foam wedges. This allows engineers to take extremely precise measurements of audio performance, unaffected by the environment they are in. After some time in the chambers, we watched some highly-technical certification testing take place.The McIntosh custom theater.
We ended the day in the McIntosh custom theater, and never have I been so happy to have the darkness of a theater room spoiled. The warm glow of blues and greens made the theater feel like something you’d experience on the Enterprise (assuming Star Fleet crews appreciate hi-fi as much as we do). After receiving our McIntosh McMasters certification plaques and thanking our gracious hosts, it was time to leave this technological utopia.
Wrapping up the trip.
We took our final bus ride back to the hotel for our last dinner together and shared each other’s company as we celebrated this wonderful experience. We parted ways in the halls of the hotel, eager for much needed sleep before we departed the next morning for our respective homes.
Meet the author: Andrew Parfitt
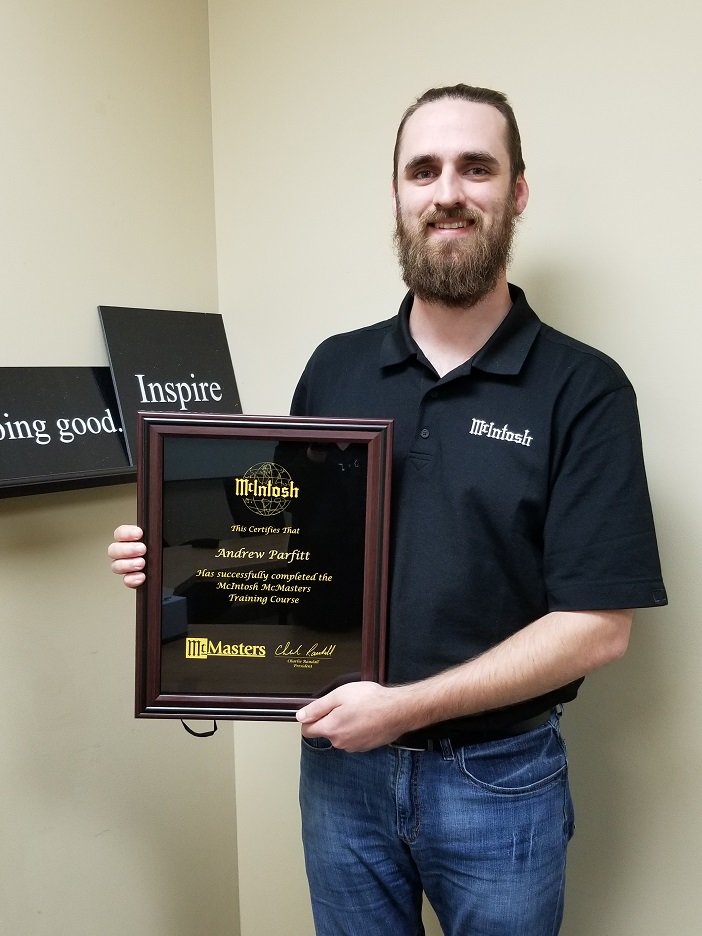
My love for cinema and music began early, and I mean that in two ways: I fell in love with these art forms at an early age, and my taste vastly predated my own era. Thanks to the influence of my parents, I grew up on the films of John Ford, Cecil B. DeMille, and Alfred Hitchcock, and listened to music greats such as Herb Alpert, Frank Sinatra, and The Beach Boys. I still hold that love, graduating with a degree in video production, interning with Walt Disney Parks and Resorts Entertainment, and now getting to design systems and spaces that bring these arts to life in incredible ways.
What's your favorite part of your job?
My favorite thing to do for my customers is create magic. I love going above and beyond to bring incredible music and audio into someone’s life. I recently had a customer who had been using entry level earbuds, but wanted more impact and detail. To provide that better experience, I hooked him up with Klipsch X12 earbuds, an Audioquest Dragonfly, and suggested switching to TIDAL HiFi streaming. After experiencing that setup, he quickly told me that I had turned him from a music lover into an audiophile. Often, I find many of my customers have become so content with the convenient, accessible .mp3 quality and inexpensive devices that they forget entirely what the music should sound like. Music should inspire you, give you chills and goosebumps, and transport you to your favorite venue or concert hall to hear all your favorites. Helping someone get that experience is what gets me out of bed in the morning.
What products are on your wishlist?
An NAD C368 BEE integrated amp, a pair of Dynaudio Excite X34 floorstanding speakers, Sony's XBR-65X900F 65" Bravia 4K Smart TV, and a Sony NW-ZX300/S Walkman.
Comments (1)
Please share your thoughts below.
LEAVE A COMMENT1 Comment
How can I take that training course.